Hardness Matters. Choose Right, Perform Better.
We offer a wide range of punches, pins, and guide components, all available in various hardness levels to suit different tooling applications. Whether you require high wear resistance for high-volume production or a specific hardness to prevent deformation under extreme pressure, our components are engineered to meet your exact specifications. Each product is manufactured with precision and quality materials to ensure optimal performance, durability, and compatibility with your die sets or custom molds.
Hardness Selection Guide
Material Type | Core Properties (Quantified) | Performance Advantages | Ideal Applications | Industry Certifications |
High-Speed Steel (ASP60) | – Hardness: 64-66 HRC – Red Hardness: 600°C – Wear Rate: 0.12 mm³/Nm | – 3.5X lifespan vs. H13 in high-temp apps – 40% lower abrasive wear | – Automotive punch dies – IC lead frame stamping – Hard metal blanking | ISO 4957:2018 AMS 6491 |
Powder Metallurgy Steel (DC53) | – Toughness: 32 MPa√m – Hardness: 60-62 HRC – Crack Resistance: ↑30% | – 80% less edge chipping – Withstands 25T+ impact loads | – Progressive dies – Heavy-gauge stamping – Shear blades | JIS G4404:2006 ASTM A681 |
Titanium Alloy (Ti-6Al-4V) | – Biocompatibility: Grade 5 – Density: 4.43 g/cm³ – Yield Strength: 830 MPa | – 55% weight reduction – Zero ion release in sterile envs | – Medical implant molds – Aerospace fasteners – MRI components | ASTM F136-13 AMS 4928 |
Stainless Steel (SUS420J2) | – Corrosion Resistance: 1000h salt spray – Surface Finish: Ra≤0.1μm – HRC: 50-52 | – 18X better corrosion resistance – FDA-compliant surfaces | – Food packaging tools – Pharmaceutical molds – Chemical processing dies | FDA 21 CFR 177.2600 DIN 1.2083 |
High-Speed Steel (ASP60) – The Wear-Resistant Champion for Extreme Conditions
Key Features & Applications:
ASP60 is a cobalt-enriched high-speed steel produced via powder metallurgy, achieving 64-66 HRC hardness and 600°C red hardness. Its uniform carbide distribution (90% improvement over H13) makes it ideal for high-speed stamping (300+ strokes/minute), such as automotive lock components and precision SIM card slot punching. It withstands continuous impact from aluminum/stainless steel, with a typical lifespan of 2 million presses. However, its cost is 2X higher than standard tool steels, making it suitable for high-value parts.
Powder Metallurgy Steel (DC53) – The Heavy-Duty Crack-Resistant Expert
Key Features & Applications:
DC53 undergoes vacuum degassing to deliver 32 MPa√m toughness (30% higher than SKD11) while maintaining 60-62 HRC hardness. Its MC-type carbides effectively block crack propagation, perfect for thick-plate blanking (≥4mm) or stainless steel cutlery progressive dies. Real-world data shows an 80% reduction in edge chipping for EV battery case stamping. Avoid prolonged use above 550°C.
Titanium Alloy (Ti-6Al-4V) – Lightweight Solution for Medical & Aerospace
Key Features & Applications:
As a biocompatible material (ASTM F136), Ti-6Al-4V prevents ion contamination in medical implant molds and reduces press inertia due to its 60% lower density vs. steel. In aerospace rivet cold heading, its 830MPa yield strength and 7W/mK low thermal conductivity prevent workpiece adhesion. Downsides: extreme cost (~6X SUS420J2) and unsuitability for >400°C environments.
Stainless Steel (SUS420J2) – The Ultimate Corrosion-Resistant Choice
Key Features & Applications:
Passivation-treated SUS420J2 resists pH1-14 corrosive media, while its Ra≤0.1μm mirror finish meets FDA food-contact requirements. Typical uses include chocolate molds (acid resistance) and PVC medical tube dies (chloride resistance). Lower hardness (50-52 HRC) necessitates DLC coatings to achieve 70% of standard tool steel wear resistance.
Download the Brochure for Free
Process Standards PDF
Ensures precision and reliability in manufacturing
Hardness Standards PDF
Guarantees product durability and strength
Material Selection Standards PDF
Premium imported materials for superior quality
Surface Finish Standards PDF
Flawless surface treatments for high-quality results
Tolerance Standards PDF
Precise tolerance control for perfect fit
Lifespan Standards PDF
Ensures long-lasting product performance
Related Products
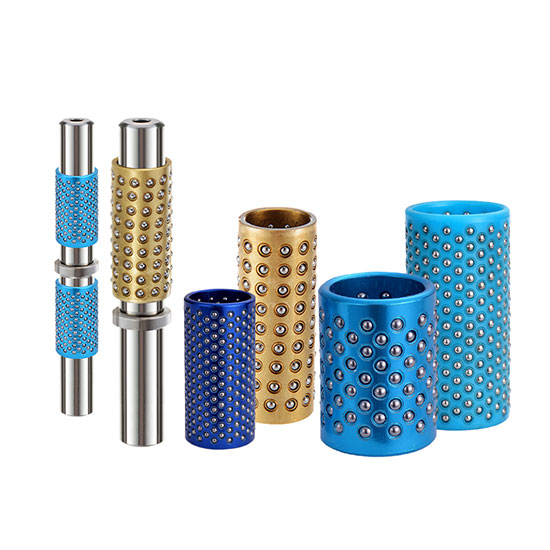
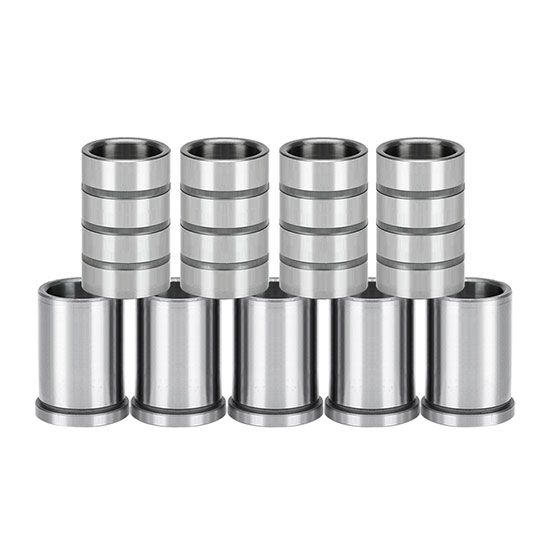
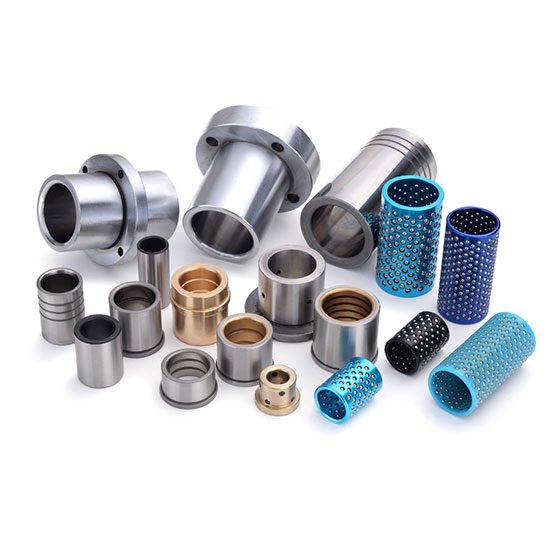
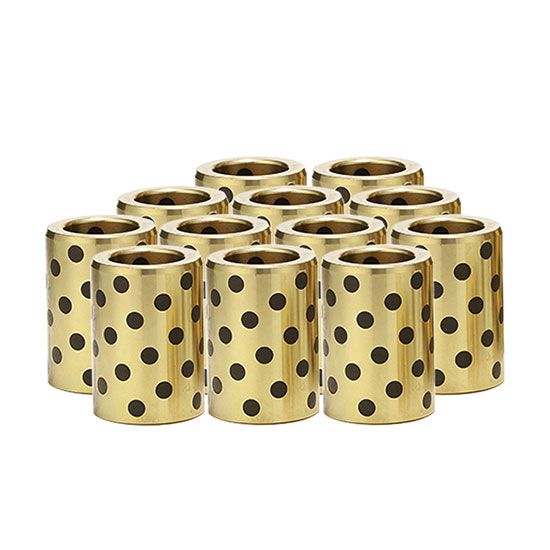
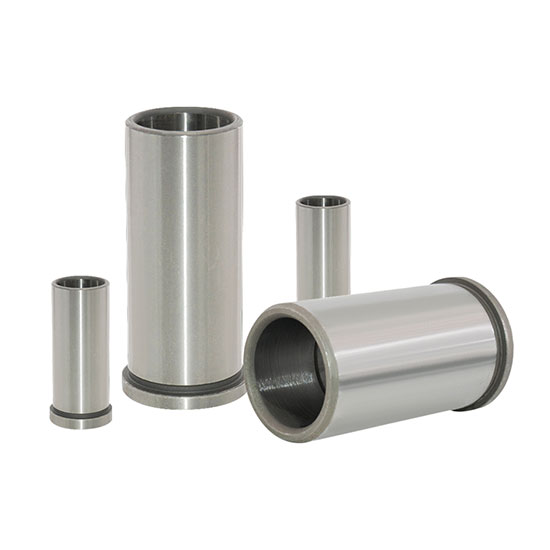
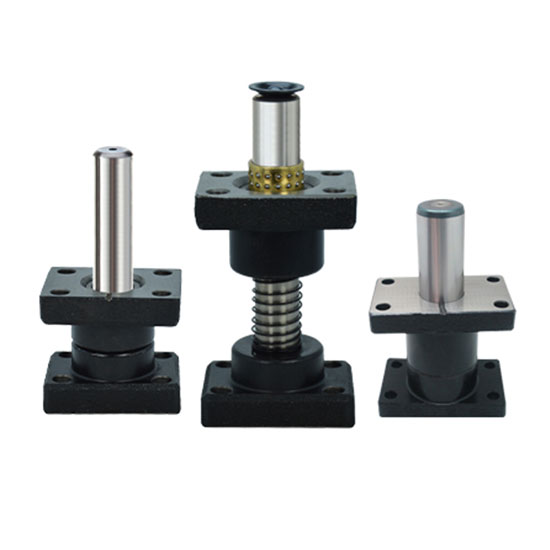
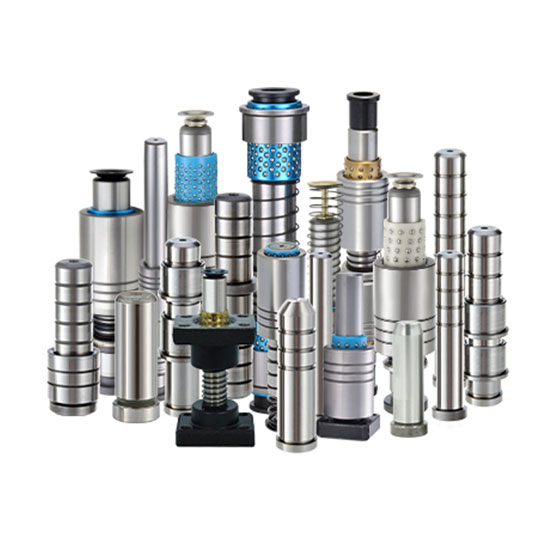
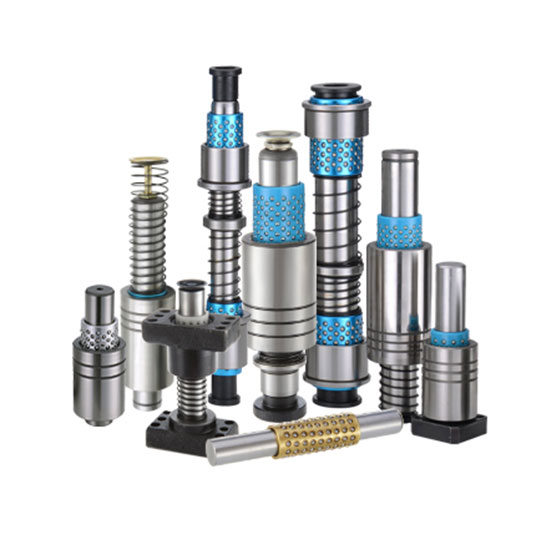
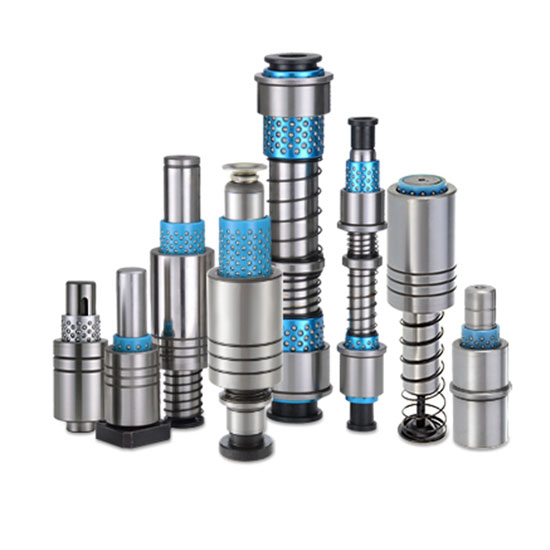
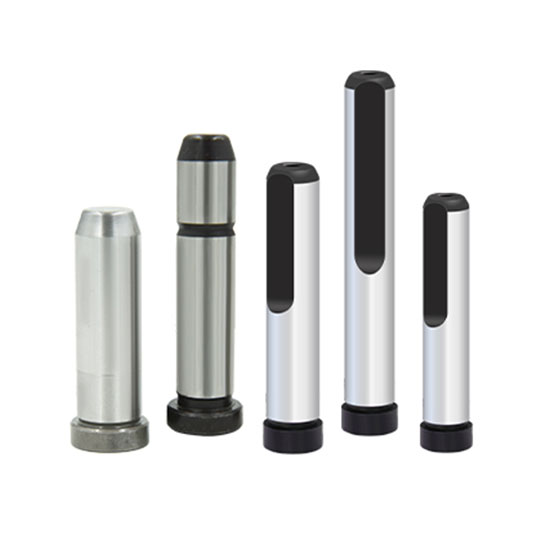
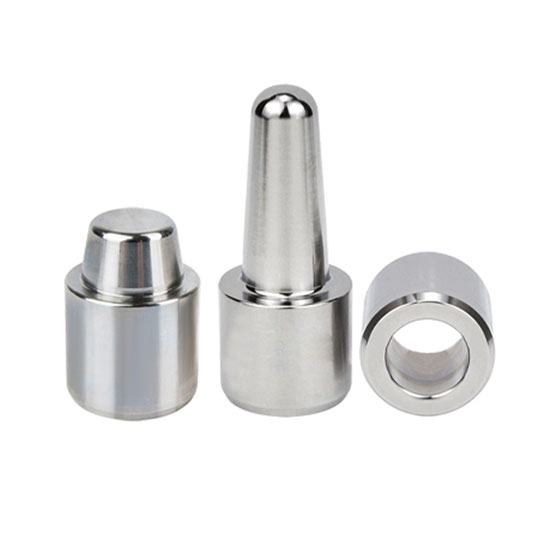
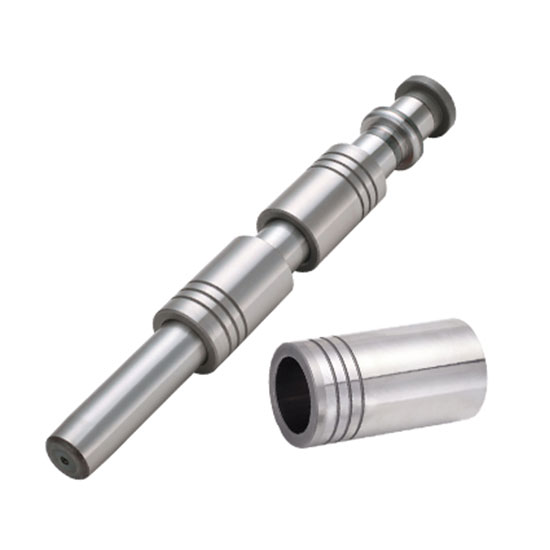
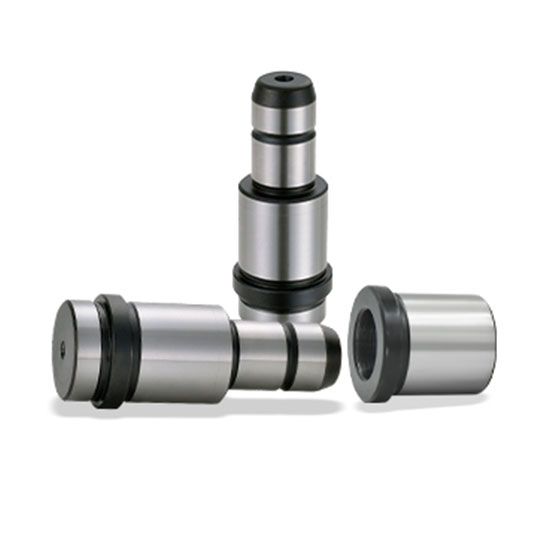

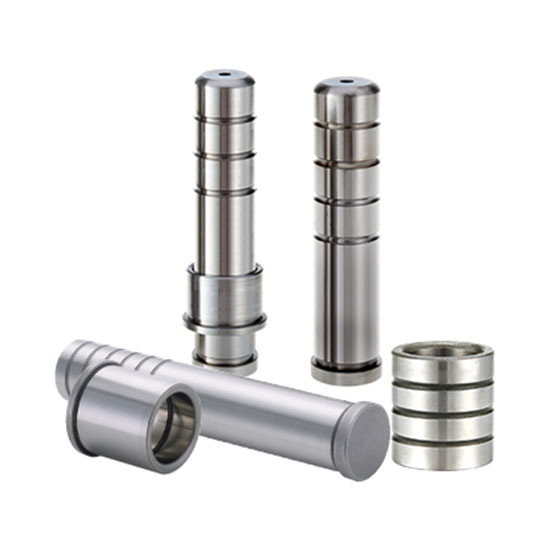
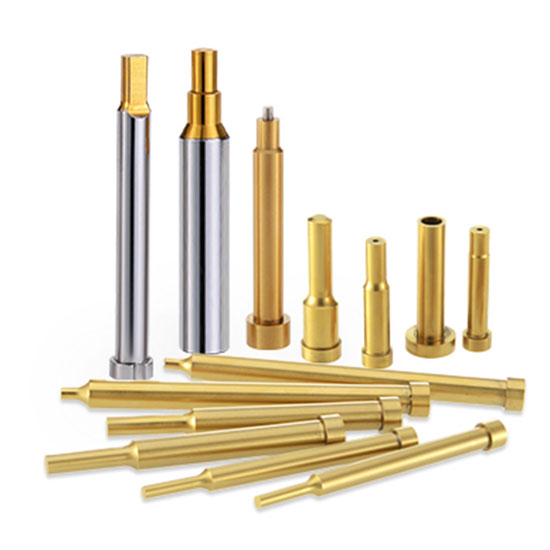
The customization process of Punch Pin
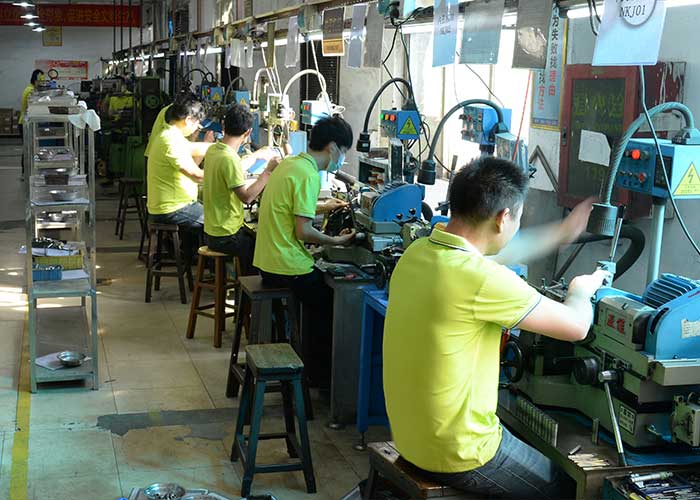
Demand confirmation
· Receive pdf/dwg/step drawings, or photos + hand drawings + main dimensions
· Provide material suggestions (for example, SKD11 is suitable for high wear-resistant scenes, asp23 is suitable for high-frequency stamping)
· Confirm whether proofing or processing of mating parts (such as stamping die) is required
Technical evaluation and proofing
· Proofing time: 3-7 working days (according to complexity) Provide inspection report / physical photos / video acceptance
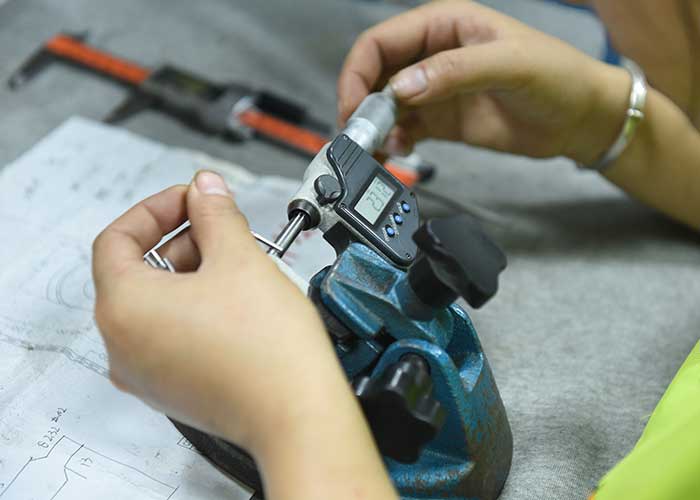
10,000 cycles
Zero wear
100,000 times
No cracks after punching
5xLonger life
Cryo-treatment
30%+
Hardness boost
3,000+
Industry clients
Quote Request Checklist
Material Specifications
Tolerance Requirements
Surface Treatment
Application Scenario
Drawing Availability (If none, describe)
The more details you share, the faster and more precise your quote will be! Looking forwarded to future cooperation.