🏥 Micro Burr Control Solutions for Medical Implants
Looking for burr-free stamping tools for medical implants? We manufacture custom punches, dies, ejector sleeves, and guide posts for use in orthopedic implant production, dental prosthetics, and surgical instruments. Our micro-deburring solutions reduce manual finishing, ensure ISO/FDA compliance, and deliver clean, precise edge control for biocompatible materials like titanium and stainless steel.
🔬 1. Pain Points in Medical-Grade Machining
Medical implant manufacturers face unique challenges in deburring and edge integrity:
❗ Microscopic burrs on precision implant surfaces can lead to:
Biocompatibility risks
Inflammation or rejection
Regulatory non-compliance (FDA, ISO 13485)
❗ Manual deburring is time-consuming and inconsistent
❗ Risk of dimensional deviation after post-processing
❗ Lack of standard tooling for micro-feature components (e.g., bone screws, plates, spinal rods)
🛠 2. Our Technical Solution: Precision Deburr from the Source
We deliver tooling and process solutions specifically designed for micro burr elimination at the stamping or forming stage, reducing post-processing time and improving implant surface quality.
🔧 All tools can be custom-manufactured based on drawings or implant part models.
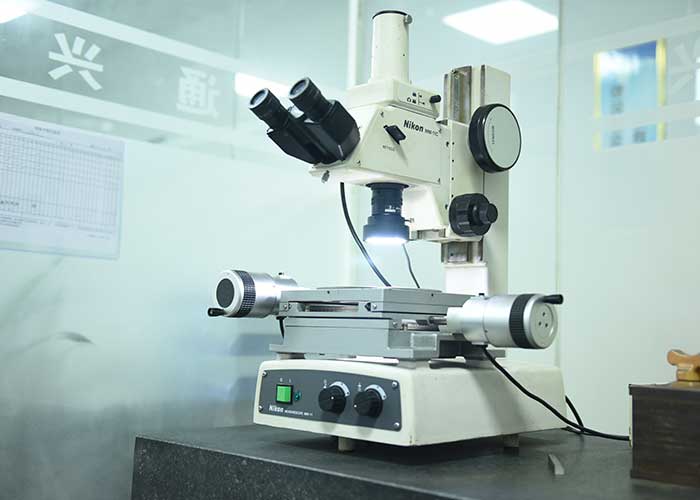
🧩 Key Technologies:
Ultra-precision punch & die edges: radius control down to R0.02mm
Special clearance optimization for titanium, cobalt-chrome, and stainless steels
Coated punches (DLC, TiCN) for anti-adhesion and low friction
Mirror polishing on contact surfaces to reduce metal tear-off
Integrated micro-deburring brush units (optional)
Support for medical-grade materials: ASTM F136, 316LVM, Ti6Al4V, etc.
🧪 3. Our Advantages in Medical Tooling
01.
Burr control under 5μm
Fully validated in real-world medical part production
02.
±0.001mm tolerance
Suitable for micro implants & orthopedic parts
03.
Material compatibility
Titanium alloys, stainless, cobalt-based alloys
04.
In-house polishing & coating
Ensure ultra-clean surface finish
04.
Reverse-engineering
Send us a worn tool or part for analysis
📊 4. Case Study: Titanium Bone Plate Blanking
Customer: Orthopedic implant manufacturer
Material: Ti6Al4V, 0.8mm
Previous Process: Manual burr removal + post-polishing
Issues:
Micro burrs up to 12μm
Unstable manual rework process
Risk of surface scratches
Our Optimization:
Provided mirror-finished DC53 punch + DLC coating
Controlled die clearance to 0.002mm
Edge rounding < R0.02mm
Results:
Metric | Before | After |
Burr Height | 12μm | ≤ 3μm |
Rework Time | 2.5 min/part | 0.3 min/part |
Compliance | Failed 2 of 5 lots | 100% pass |
Quote Request Checklist
Material Specifications
Tolerance Requirements
Surface Treatment
Application Scenario
Drawing Availability (If none, describe)
The more details you share, the faster and more precise your quote will be! Looking forwarded to future cooperation.
📩 Get Precision You Can Trust
📥 Upload your part design or photo of burr issue
💬 Get a deburring strategy and punch die quote within 24h
🏭 Factory-direct, medical-grade tooling customization