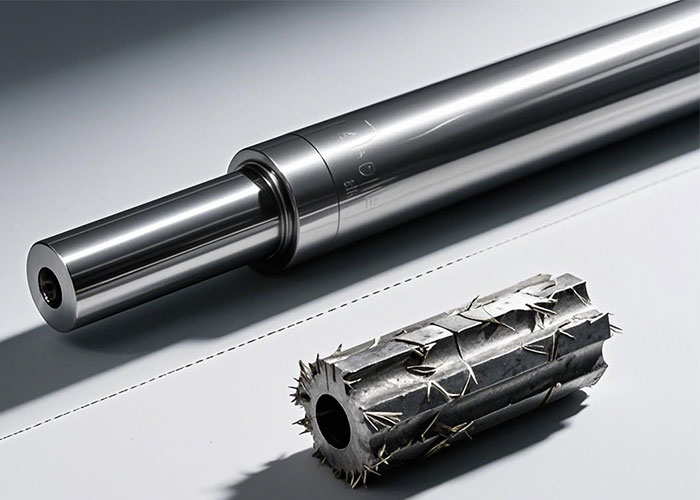
Burr Issues -The Hidden Cost Driver
Burrs increase defect rates by 30-50% and add 25% post-processing costs for manual deburring. These micro-imperfections trigger chain effects: reduced assembly accuracy, accelerated wear, and even end-product failures. HTX’s 5D Burr Control System helps clients maintain burr-related defects below 0.5% while eliminating 90% secondary processing, achieving dual optimization of quality and cost.
Why Stamping Burrs Happen?
Factor | Mechanism | Experimental Data | Optimization |
Clearance | Excessive gap causes material tearing | 5%→8% material thickness → Burr height↑120% | Maintain 6-10% material thickness |
Insufficient gap accelerates wear | (Low-carbon steel, 2mm, HTS 2022) | Dynamic thermal compensation | |
Speed | High speed induces material flow instability | 200→500spm → Burr probability↑40% | Optimal range: 300-400spm |
Low speed causes secondary shearing | (304 stainless, HTX case study) | Servo presses recommended | |
Material | Higher hardness → cleaner shear surface | HRC50→62 dies → Burr rate↓35% | Powder steels (e.g., ASP60) |
Hardness | Over-hardness leads to edge chipping | (1.5mm copper alloy, JMP analysis) | Target HRC58-62 |
Die Steel | Low hardness causes plastic deformation | SKD11(HRC58) vs DC53(HRC62): 2.8x burr difference | TiAlN coating for longevity |
Hardness | Micro-cracks initiate burrs | (500k strokes tracking, JFMA 2021) | Laser cladding maintenance |
Probability of burr formation in different hardness mold steels
Steel Type / Hardness | Typical HRC | Burr Formation Tendency | Notes |
SKD11 (Cr12Mo1V1) | 58–62 HRC | 🟢 Low | High wear resistance and edge retention, ideal for fine blanking. |
DC53 | 60–62 HRC | 🟢 Low | Tougher than SKD11; less chipping, good for high-precision stamping. |
D2 Tool Steel | 58–61 HRC | 🟡 Medium-Low | Excellent wear resistance, but slightly more brittle. |
HSS (High Speed Steel) | 62–68 HRC | 🟢 Very Low | Excellent edge sharpness, minimal burring, expensive but premium. |
P20 (Pre-hardened steel) | 28–35 HRC | 🔴 High | Soft material; wears quickly, causing burring in mid/long runs. |
S50C (Medium Carbon Steel) | 45–50 HRC | 🔴 High | Lower hardness leads to faster edge wear, especially in high-speed stamping. |
Tungsten Carbide | 80+ HRA | 🟢 Extremely Low | Ideal for zero-burr blanking, but very brittle and costly. |
SKH-9 / SKH-51 (HSS variants) | 63–66 HRC | 🟢 Very Low | Excellent for long-life precision stamping with minimal burrs. |
Our Solutions - 5D Solution System
Technology | Key Innovation | Performance Metric |
Edge Geometry Engineering | Asymmetric cutting edge design | ↓35% burr occurrence |
Coating Optimization | Nano-composite friction-reduction layer | Coefficient of friction ≤0.15 |
Clearance Control | Real-time adaptive gap adjustment | ±0.003mm precision |
Surface Micro-Treatment | Mirror-polishing technology | Surface roughness Ra≤0.1μm |
AI Monitoring | Predictive burr formation alerts | 98% detection accuracy |
Strict Quality Control
Our Special Process Capabilities ensure unmatched precision and durability. We use advanced technology and craftsmanship to meet strict quality standards, delivering reliable, high-performance products every time. Trust our experience to exceed your expectations.
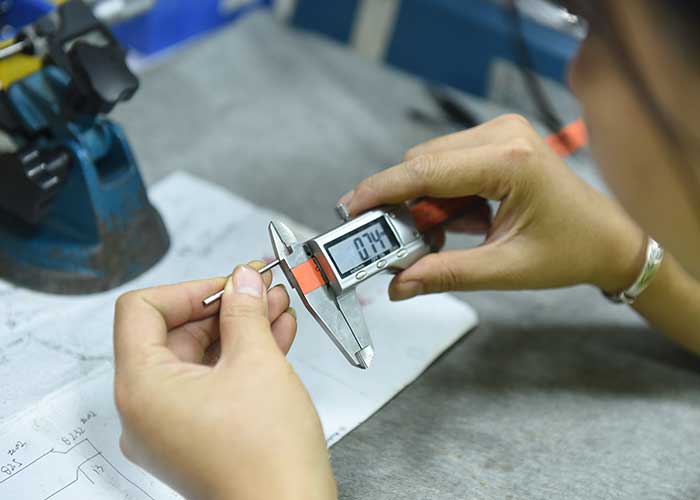
Diameter Check
Accurate diameter measurements with a tolerance of ±0.002mm.
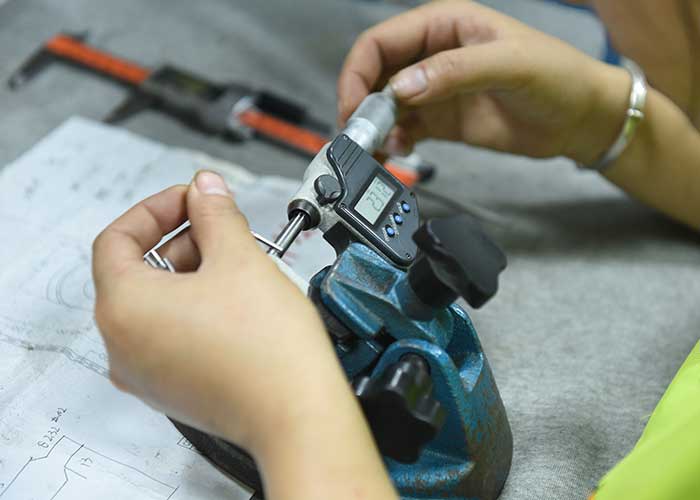
Length Check
Precise length measurements to ensure accuracy.
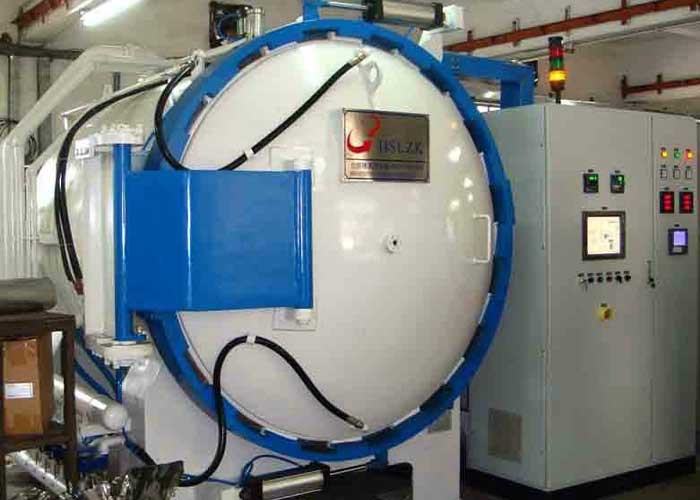
R Check
Checks radius and curvature with high precision.
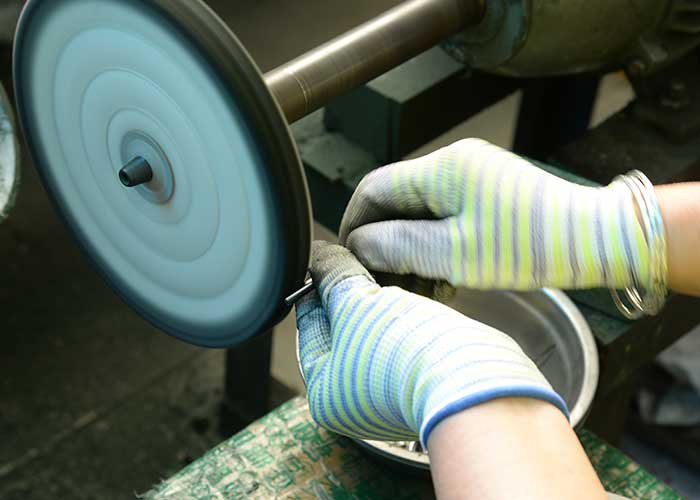
Surface Finish
Inspecting surface finish for smoothness and flawless surfaces.
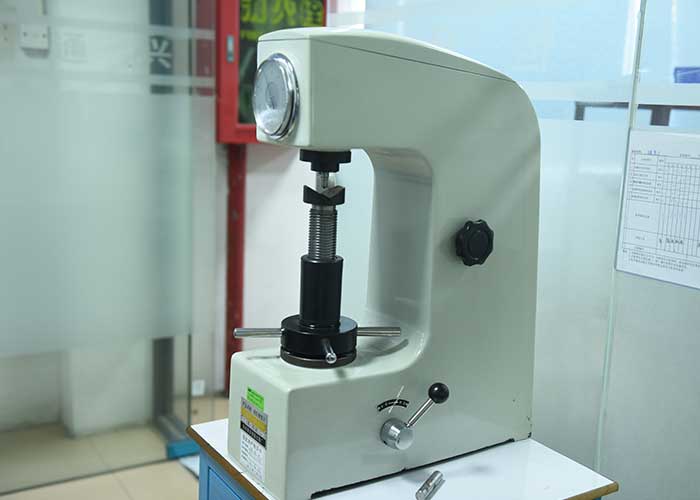
Hardness Test
Ensuring materials meet required hardness standards.
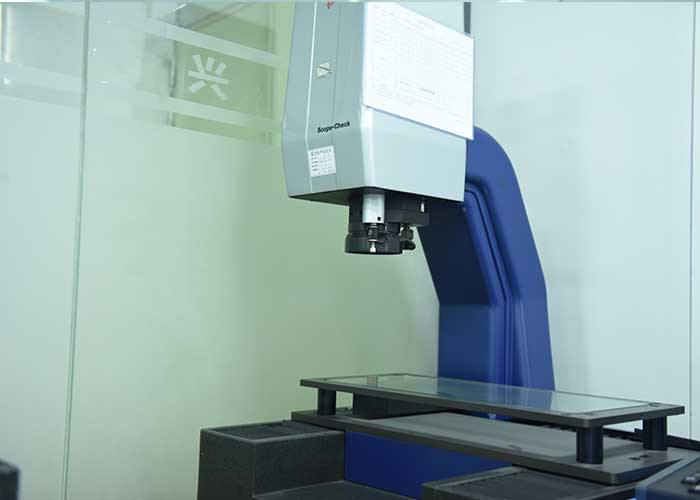
Vertical Check
Verifying verticality with precise 2D equipment.
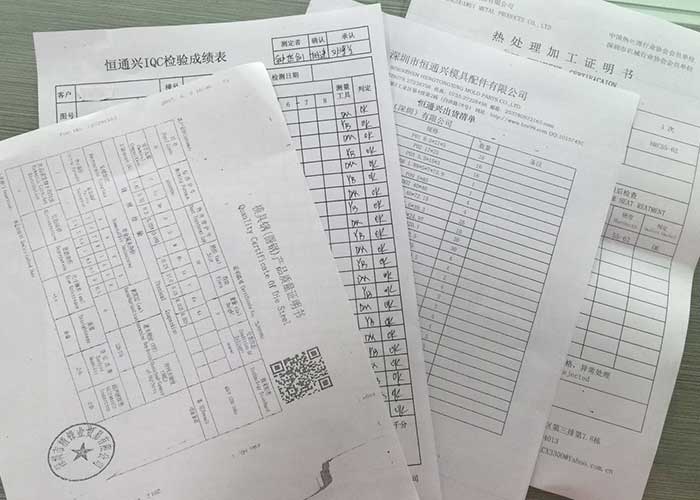
Inspection Report
Each product is shipped with a detailed inspection report.

Packaging
Cleaned, labeled, and safely packed for secure delivery.
Solution Validation: Benchmark Test Results
Metric | Before Optimization | After Optimization | Improvement | Verification Standard |
Defect Rate | 8% | 0.50% | ▼93.75% | ISO 9001 QMS |
Production Efficiency | 2,000 pcs/hour | 3,000 pcs/hour | ▲50% | Industry Baseline |
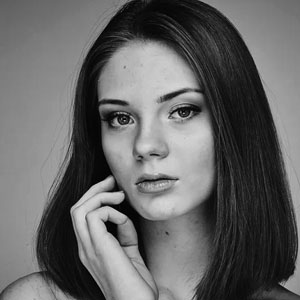